Thursday, February 26, 2009
Highway 2.0
Vacant land along Americas interstate highway system is renewed through the growing of quick-cycling biomass crops and the installation of wind turbines and solar photovoltaics. This represents an entirely new economy: Interstate Energy Farming. A redeveloped interstate corridor would be the backbone of an adaptive landscape reuse strategy on a national level.
http://www.youtube.com/watch?v=AP80j_mz4Jo
Monday, February 23, 2009
Yestermorrow Instructor Thea Alvin Featured in Vermont Magazine
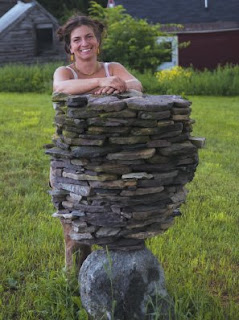
Quite the world traveller, "..she was recently in Arizona, leading a seminar of executives in the intricate skill of building a stone arch (the lesson— out of hard work comes balance and harmony). She was recently in England,finishing a grotto at a country estate. She spent a month in China, where she built ten arches from bricks, tiles, slate and marble. She also has built stone sculpture in Canada, France and Italy; in fact, Thea wants to travel the world, leaving works of stone art behind."-- Vermont Magazine, March/April 2009
Friday, February 20, 2009
Economic Stimulus Bill Initiatives for Home Energy Efficiency
Wednesday, February 18, 2009
A note from a former student and intern
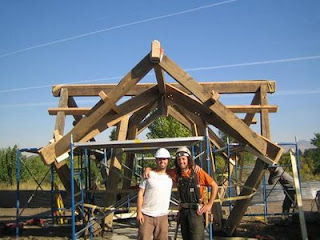
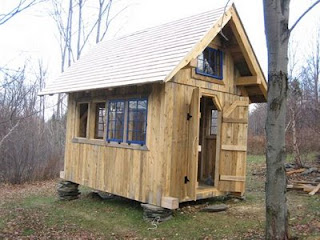
Tuesday, February 17, 2009
Mooooose!
Timberframing Part 2: Laying Out/Cutting a Tenon


There's more to layout than what's shown and you'll want to do all of that before cutting, but for simplicity, I'll move on. The first cut is with a carpenter's crosscut saw. It's pretty hard to do well and I have a lot to improve technique-wise.

After planing, I removed the parts of the tenon that will make it 4.5 inches across as well as the housing that will help the tenon slide right into it's mortise. A slight taper on the tenon's faces, chamfers on it's edges and ends, and a peg hole and it's all done.
I'll post some photos from our shed raising in the next and last edition of my timberframing overview - probably next week.

Tuesday, February 10, 2009
Living Big in a Small World
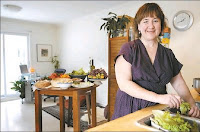
"When Moneca Kaiser talks about smart home storage ideas, she has the voice of authority. Hardly surprising. The owner of Moneca Kaiser Design Build (www.mkdesignbuild.ca) lives in a 325-square foot apartment. What’s more, she works from her east-end home and is so efficient at keeping things tucked away that, last Sunday, she hosted a Chinese New Year’s party for 25 friends.
For Kaiser, a committed environmentalist, good storage starts with minimizing possessions. That said, she does have stuff. Office supplies, for example. To keep her home looking mostly like a home, she stores business items in a repurposed chest of drawers, using dividers to separate pens and pencils from sticky notes. Other supplies, including paper and envelopes, are easy to find in see-through plastic bins stacked on closet shelves. Paper clips sit in a magnetized cup on the side of her work table. “If you have limited space,” she says, “you have to be very thoughtful about what you need to have, not what you want to have, at your fingertips.” Files and other items sit in wicker chests that she bought at Pier 1. Like many other items in Kaiser’s apartment, the chests do double duty as end tables or night tables when needed. While she did once own a standard bed with all sorts of things stashed below in pull-out storage containers, Kaiser now uses a futon on the floor, complemented by a Persian rug with plenty of cushions. “I love that Asian feeling. It makes everything feel so much bigger.” She also found an inexpensive pine wardrobe at IKEA with sliding, glass-panelled doors. She can put her futon up against the wardrobe and still have easy access to the contents."
To read the full article, visit: http://www.pressdisplay.com/pressdisplay/viewer.aspx
From Brooklyn to Blogosphere...
Hey, old-house renovators from Brooklyn to the Hudson Valley: wouldn’t it be great if there was, like, a school you could go to for anywhere from 2 to 12 days to get some hands-on, experiential learning in building design and construction?
And what if it was located in central Vermont’s Mad River Valley, and wasn’t too expensive, and the food was good?
There is such a place: it’s called Yestermorrow Design/Build School, and since 1980, it’s been offering courses in all aspects of the building arts and trades to students, homeowners, architects, and builders on its 38-acre campus. The instructors are all pros in their fields, and the teacher-to-student ratio is high.
Read the whole post at http://casacara.wordpress.com/2009/02/10/renovation-education/
Monday, February 09, 2009
Visits
* Frost protected, insulated slab foundation is “greener” than a full foundation
* Radiant heat floors in upstairs and downstairs zones
* Solar orientation – large windows on south allow sun in to heat thermal mass of concrete floor/slab in winter; overhangs provide shade in summer
* Airlets in each room and bathroom fans with timers for full-house ventilation
* Larsen truss framing system with rough sawn local hemlock
* Upstairs space is independent of downstairs (gasket on door, separate heat, ventilation)
* No plastic vapor barrier – used special primer on all inside walls for vapor barrier
* No window trim on outside or inside of house cuts costs but looks great
* Structural "novelty" siding thicker means sheathing underneath not needed
* Continuous insulation envelope – blown cellulose insulation is also treated with borate for fire retardation and critter-proofing
* Tile work acts as a heat shield for wood stove, tub surround, shower walls, window sills
* Chimney blocks dry stacked with mortar on outside
* Cost of house was approximately $100 per square foot!!
This weekend, I hosted my sister, Anna, at Yestermorrow. She came up to ski and stayed with me on campus for a few days. Much as I was inspired by Carol Thompson's home, my sister oohed and ahhed her way around the Yestermorrow campus. She wanted her picture taken in the treehouse, she exclaimed that the wooden pegs and cob bench in the timberframe cabin were "really cool," and she was duly impressed by the lack of any offensive odor issuing from the [very full] humanure toilet in my living quarters in the chalet. When she left, she commented on how refreshingly different everything and everyone was here compared to "back home" in suburban Philadelphia. If only we can get more urban and suburbanites thinking about how their built environment and communities can better relate to and work within the balance of nature...
Which brings me to the owl I encountered today. I was walking at dusk, when I saw a large, fluffy, gray bird wing across a field and alight on an electric wire. When I recognized the bird as an owl, and I felt overwhelmed with good fortune and awe. "You're beautiful!," I exclaimed aloud to the bird. In response, the creature cocked its head and peered at me with its piercing eyes. Beauty, grace and elegance collided in the timeless gaze of this animal, which seemed to say both, "I know," and "What are you doing here?" My answer: I am yet striving to learn how to achieve the natural harmony and balance that you, owl, so perfectly embody.
Spring?
The recent rain has turned our snowshoe trails into rock hard roads and our old boot prints into potholes, so I was taking it kind of slowly today. Halfway through my descent, I detected movement below me. At first, I thought it was another intern poking around the trails, but it was a whitetail deer foraging the places where the snow has worn away to brown and green again. Upon watching her for a moment, I noticed more deer. There were actually five in a line working their way across the slope below me. They hadn't seen me yet, so I was able to observe their activities unnoticed. Once I continued down, they saw me and bounded off to the south, their white tails bobbing up and down like flags behind them. I stopped to watch them go, and the crunch of our fading footfalls gave way to the soft burbling of springs converging just down the trail.
Sunday, February 08, 2009
Timberframing Intro : Part 1

Timberframing is basically the joining of timbers (cut logs) to form a framework for the creation of a structure like a house, shed or barn. I like to think of it as furniture quality joinery for the purposes of making a beautiful, hearty and safe building.
There are two basic methods of working through laying out and performing the joinery in a timber frame building: scribe rule and square rule. Jack Sobon's works are great resources for learning more about these techniques. Scribing means that timbers are mated by placing them near each other and marking the timbers to follow the natural contours of the each. This means that each timber will only fit well in one particular place in the building and all members must be marked so that the puzzle can be put together properly at raising time.

To use the square rule on a timber, you must first make a thorough inspection of the sides to try to determine which two adjacent sides are closest to being square with each other. Your sawyer should be able to cut the logs well enough for this to be possible on at least two sides. We used framing squares for this as well as for nearly all of our layout tasks. Once you've determined the two squared sides, make black triangles on those sides pointing to their common corner along the timber. These sides of the timber are your reference edges from which all joinery will based.
Our joinery was specifically designed to take advantage of the framing square as it uses many 1.5" and 2" dimensions which match the widths of the two legs of the framing square (as well as the 1.5" and 2" chisels we used). As a side note: If you're using a newer framing square, make sure your legs actually match this dimension instead of taking it for granted. One of my classmates had a brand new square that was slightly bigger than these standard dimensions.
Next time, I'll talk about crucial dimensions and laying out some joints.
Friday, February 06, 2009
Tax Credits for Energy Efficiency Improvements
Wednesday, February 04, 2009
How has Yestermorrow impacted YOU?
We hope to profile members of the Yestermorrow community in our upcoming newsletters and on our website. If you can offer a testimonial, please email Kate Stephenson (kate@yestermorrow.org) and if possible, include pictures of you and/or your project(s).
Thanks!
Kate
Thinking about the Yester-garden...
Handheld snips/pruners (2)
Broadfork
Soil thermometer
More coldframes
Hula/Stirrup hoe
Hori Hori Garden Knife
Vermiculture supplies (worms!)
Twine tape and twine
Soil Test Kits
Compost
Potting soil
Germinating Mix
Misc Seed Trays and Transplant pots
Black plastic
Concrete reinforcing mesh
Watering can
Garden gloves
Aerator for compost tea